Wide Belt Sander findustry 1352
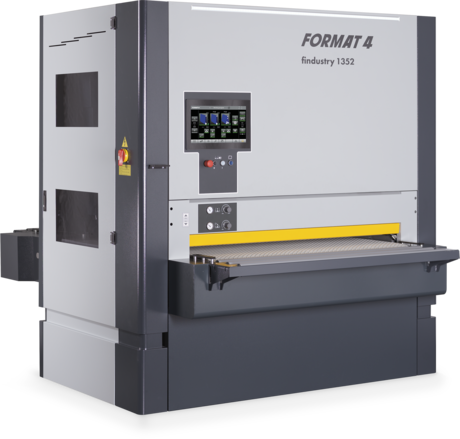
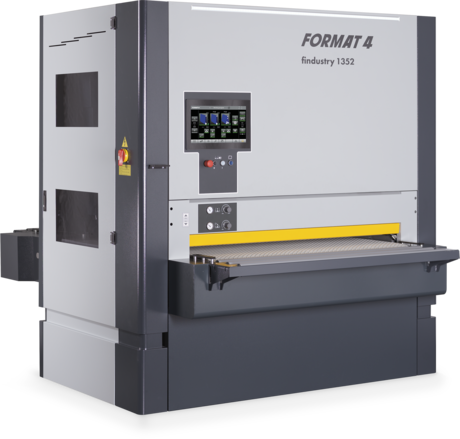
Industrial top performance, freely configurable
FORMAT4 findustry 1352 | 1353 | 1354 - The new wide belt sanding machines for individual requirements
The new FORMAT4 wide belt sanding machines findustry convince in industrial use above all by the individually configurable combination of the units. The machine can be equipped with two, three or four units, precisely adapted to the specific use and the respective field of application. Thus, a high degree of customisation guarantees that all requirements are met with regard to surface finish and processing efficiency.
Maximum operating comfort in industrial use.
The clearly structured touch screen control can be operated intuitively. All machine functions are clearly shown graphically on the digital display. The infeed thickness can be set to the tenth of a millimetre directly from the control panel at the touch of a button. The automatic thickness measurement facilitates adjustment of the machine to the desired workpiece thickness. The workpiece is measured without any additional measuring devices and the thickness is then directly transmitted "wirelessly" to the machine. A vacuum table, table extensions with rollers on the inlet and outlet sides as well as optional pressure shoes on the sanding units ensure the best possible comfort and ideal machining conditions for workpieces in every format.
FORMAT4. Uncompromising expertise for the highest of requirements
The Felder Group premium brand has met the highest standards of professional users since 2001. The customised high-performance solutions are uncompromisingly innovative, offer maximum operating comfort and complete productivity.
The most important highlights at a glance
Variants
Models- Your benefits
... FORMAT4 Premium machines for premium requirements

- Constantly high performance in industrial continuous operation
- Customer specific optimised production solutions
- Solid design with premium components
- Many variations of specification packages with high-tech solutions
- Complete engineering precision
- Premium user comfort
- Award winning design
- Quality and precision from Austria
- Uncompromised productivity
- Perfect service package before, during and after the purchase
- Tailor made financing solutions
Details
The planet sanding unit achieves a perfect finish, especially with crossed grains. The texturing, edging and sanding of these grains is retained, thus achieving a homogeneous superfinish of the surface. The respective, individually replaceable brushes, which are arranged like a planetary system, can be replaced separately and thus allow even more flexibility and diverse production applications.

As standard, the feed speed can be continuously adjusted from the control panel between 2.8–20 m/min. The fixed infeed table height of 900 mm guarantees simple and effortless work. Due to the consistent height, the machine can also be integrated into a processing line without any effort.


Automatic thickness measurement facilitates adjustment of the machine to the desired workpiece thickness. The workpiece is measured directly on the machine without additional measuring devices being required. The required sanding depth can be set in + or - using the adjustment wheel. This wireless option makes it possible to measure the workpiece in front of the machine. The thickness is transferred wirelessly to the machine.




With a segment width of 27 mm and innovative silicone technology, the electro-pneumatic segmented sanding shoe ensures optimum sanding results and lower compressed air consumption. The pressure of the sanding pad can be individually adjusted in increments of 0.1 bar from the machine infeed side.


The cross belt sanding aggregate which is included in the standard equipment and equipped with an electro-pneumatic sanding pad and chevron belt, is particularly suited for the processing of lacquered surfaces and high gloss production. Rough wood fibres that cross the grain are removed by the sanding belt and the subsequent wide belt then smoothes the surface. The cross sanding direction ensures that there are considerably less wood fibres and that a noticeably smoother end result is achieved.
The completely uniform pressure, levels out all oscillation marks and guarantees a homogenous sanding result. An electro-pneumatic sanding belt oscillation ensures optimal centring and smooth running. Cutting speed 3 - 22 m/s, sanding belt 150 x 5000 mm.



As an option, we are able to equip your Format4 wide belt sander with roller extension tables both on the infeed and outfeed side.

These can be added to every sanding aggregate and enable a uniform pressure on the workpiece against the feed table, which is particularly important for thin workpieces. Additionally it also reduces the minimum length of the workpiece that can be processed.

The Superfinish Unit features a sanding cushion with a felt glide coating (chevron belt). This glide belt applies an even softer sanding pressure on the workpiece and is used predominantly for the sanding of lacquered workpieces and for high-gloss materials. The completely uniform pressure, levels out all oscillation marks and guarantees a homogenous sanding result. An electro-pneumatic sanding belt oscillation ensures optimal centring and smooth running. Cutting speed 2.4 - 19 m/s, sanding belt 1370 x 2620 mm.

Customer service & maintenance

Do you have any questions?
Showrooms
Issa Group International Details
Khiljan Street, George Issa Bldg
Fanar
Tel.: Mobile +961 716 000 22
Fax: +961 369 3313 108